Innovating into the future
- Details
Tradition still plays a major role in the yacht building trade. The use of a wide range of materials, the broad knowledge required by everyone and the wide variety of technologies have to meld together to create a unique, high-quality and reliable product.
So far, so familiar. But when you see that series are small, automation rates are low, that there is little scope for basic research and the supply industry can also offer limited support due to its small scale, it requires a lot of human talent and commitment to ensure the further development of the industry. Innovation is an elementary part of the day-to-day process and is best viewed from two aspects: product and process. By innovating in a smart way, one benefits from the other.
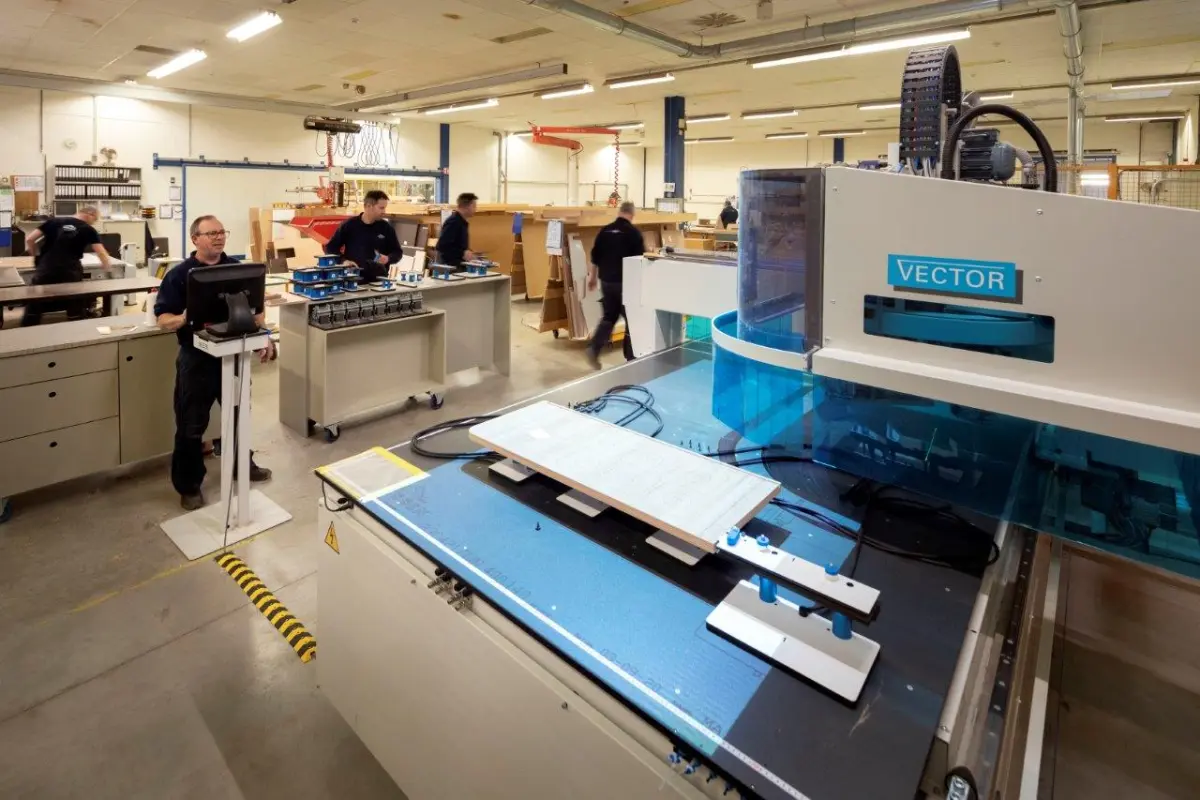
Due to its small-scale nature, yacht building almost always trails behind industrial developments, while the technologies used are familiar to many as they begin to gain importance in businesses, offices and homes. Once you have experienced its conveniences and advantages, you may also ask: why don’t I see this in my yacht or its manufacturing process to some extent, if at all?
The main reasons are scale, usability and specific knowledge. After all, all these technologies require a decent degree of repetition, it must be possible to use them meaningfully at low numbers, and someone has to master this specific knowledge within their existing range of knowledge and tasks.
Although we can’t move at the speed of big industry, we do have an innovation agenda that is constantly evolving. We are in regular contact with fellow regional companies, educational establishments and suppliers to keep up to date and see what opportunities the future holds for us.
Innovations in steel
Among other things, we follow innovations in steel production. Can we build lighter products using the latest construction technologies, calculation methods and materials? And what machines are available to us that it makes sense to use to automate the welding process or increase welding quality, for example?
There is also a lot going on in the area of coatings. We are closely monitoring developments such as robotised blasting or spraying of steel hulls, more efficient paint spray pumps, more precise and finer atomising paint guns, heated paint lines, automated mixing and heat recovery in the spray booths. To take the next step, we consider when an innovation would be applicable and whether the break-even point of the investment is not too far away.
Innovations in woodworking
In the woodworking industry, better and faster machinery is available with more features and intelligence. Although we have been automating the front end of our furniture-making process (with an automatic sheet feeder and CNC nesting milling machine) for many years, innovations are also emerging in this area. It starts with the latest design and CNC programming software that makes processes run more smoothly. The machines are becoming faster, more sophisticated, more reliable and easier to operate and therefore usable in more applications. Whereas in the past it was mainly large parts that were machined, this is now done with every part down to the smallest detail. This is completed by the edge veneering machine that automatically covers even the edges of round, oval, bevelled, straight or sharp parts. You can clearly see from our interiors how this has boosted quality, further extending the life of the yachts. Thanks to the impressive continuing development of the furniture module construction process, this leads to short work processes on board, where machining work (sawing, planing, sanding) is hardly required any more. In addition, we can see 3D digital work information slowly replacing paper work instructions and drawings.
Innovations in technology
A similar process is taking place in our technical department. Right from the design phase, engineers are working closely with steel and furniture developers so that every opening or even the smallest hole is made by CNC machines rather than by human hand. This is faster, more accurate and less demanding for humans. More and more separate operations are being combined into a module. The basis for this is created in our furniture factory and holds all the necessary assembly details. These modules are built in a dedicated unit outside the boat so that logistics and work instructions can be digitally controlled to best advantage – once again, faster, more accurate and less demanding. The fact that it’s the better craftsmen who like to work in this process and we can therefore select the best employees is a great additional advantage.
The added value for you
Of course, you, the reader, will be wondering: that’s all very nice, but what good is it to me? Well, it is of course also about adding value for the customer. What could this added value be? Series construction and our high level of experience, combined with extensive further development and automation, are creating a better product! Various aspects play a role here: reliability through precisely defined construction methods, long service life and low maintenance costs through detail quality, refined finishing through high machine utilisation in processes and systems that have been developed down to the smallest detail. But this added value for you is also determined by your yacht’s high residual value or low loss of value through integral product quality, user safety through well thought-out solutions, and an excellent image through all the aforementioned properties together.
There is also – we hardly dare mention it – the subject of sustainability, now unfortunately “elevated” into a catch-all term. The fact is that carbon emissions from production and use are very modest if you are making an intrinsically good product by having a highly effective and efficient process and treating people with respect. The product will then last for at least 50 years with relatively limited maintenance. Also, it won’t age with normal maintenance, including visually (despite trends). As a result, such a product can be enjoyed for decades without requiring any special physical, financial or environmental interventions. You can call that sustainable, can’t you?
So far, only process innovation has been covered in the above article. Substantive product innovation is a topic in its own right, which we would like to elaborate on in a future issue of the Linssen Magazine. We will then walk you through the way we see the evolution of “our yacht of the future”. Will you be reading along then?